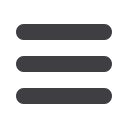
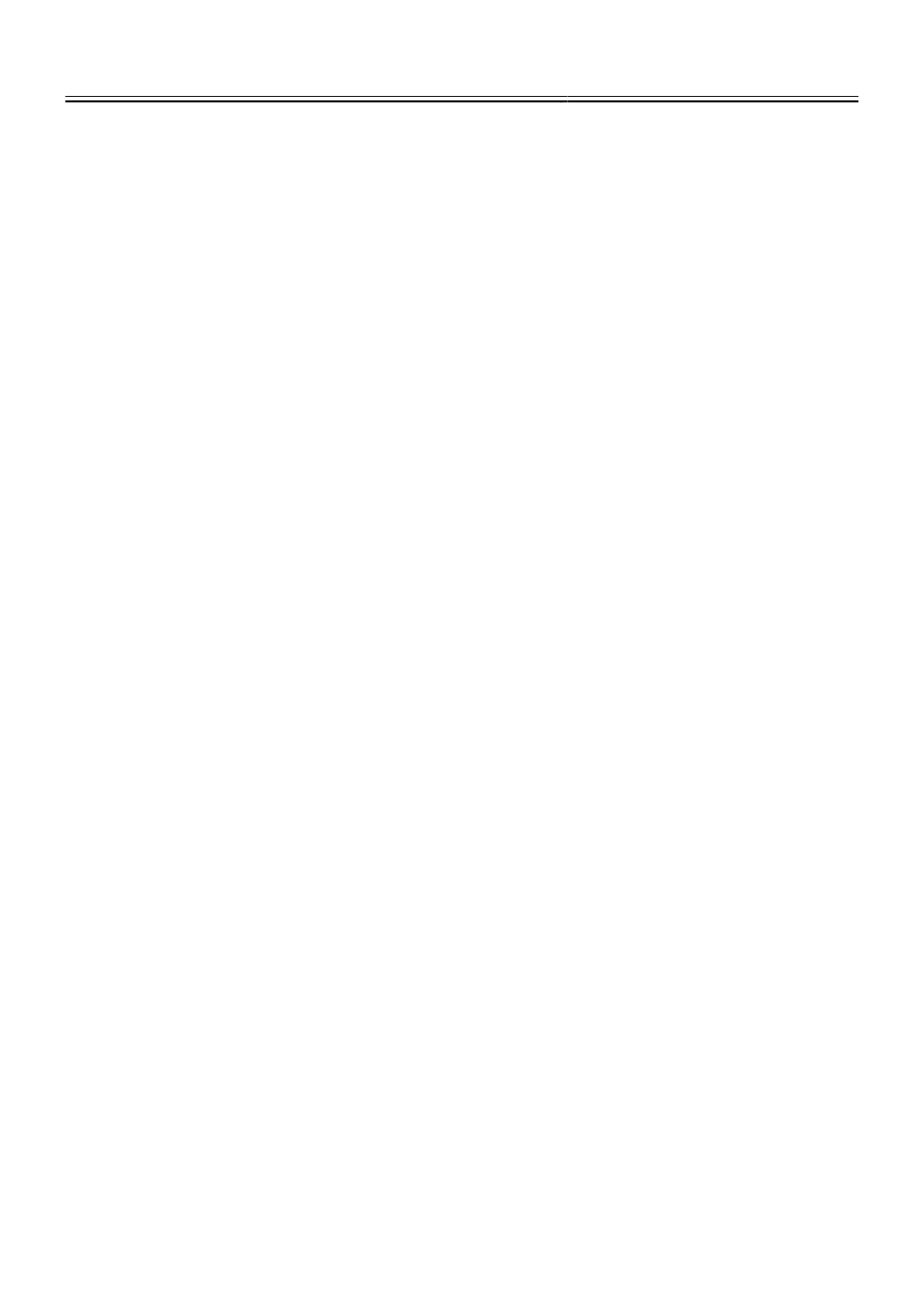
Actual Problems in Machine Building. 2015. N 2
Innovative Technologies
in Mechanical Engineering
____________________________________________________________________
120
THE STUDY OF THE INFLUENCE OF THE TOOL PATH ON THE ROUGHNESS
OF THE TREATED SURFACE IN MAGNETIC-ABRASIVE MACHINING
Ikonnikov A.M.,
Ph.D. (Engineering), Associate Professor, e-mail:
iamagtu@mail.ruGrebenkov R.V.,
Master’s Degree student, e-mail:
sigaset@yandex.ruSilivakin V.S.,
Ph.D. student, e-mail:
lg-kp@yandex.ruI.I. Polzunov Altai State Technical University, 46 Lenin Prospekt, Barnaul, Altai region, 656038,
Russian Federation
Abstract
The authors conduct designed experiments to ascertain the most efficient method of magnetic-
abrasive machining. Workpiece surface machining along and across the roughness marks at an
angle of 45° to the marks is investigated. In magnetic-abrasive machining of a workpiece the final
finish value will depend on the size of surface asperities before machining, on the direction of the
feed movement as well as on the processing time. An experimental setup was developed. Each
specimen was machined 4 times for 15 seconds. After each stage of processing, roughness was
measured on the profilograph-profilometer. The results obtained in the experiment are presented by
graphs. After the experiment it was concluded that magnetic-abrasive machining of workpieces
across roughness scratches is the most productive method in contrast to the longitudinal machining
under the same initial and processing conditions.
Keywords
magnetic-abrasive machining, surface roughness, duration of treatment, the direction of
machining, machining performance