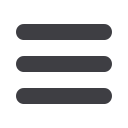
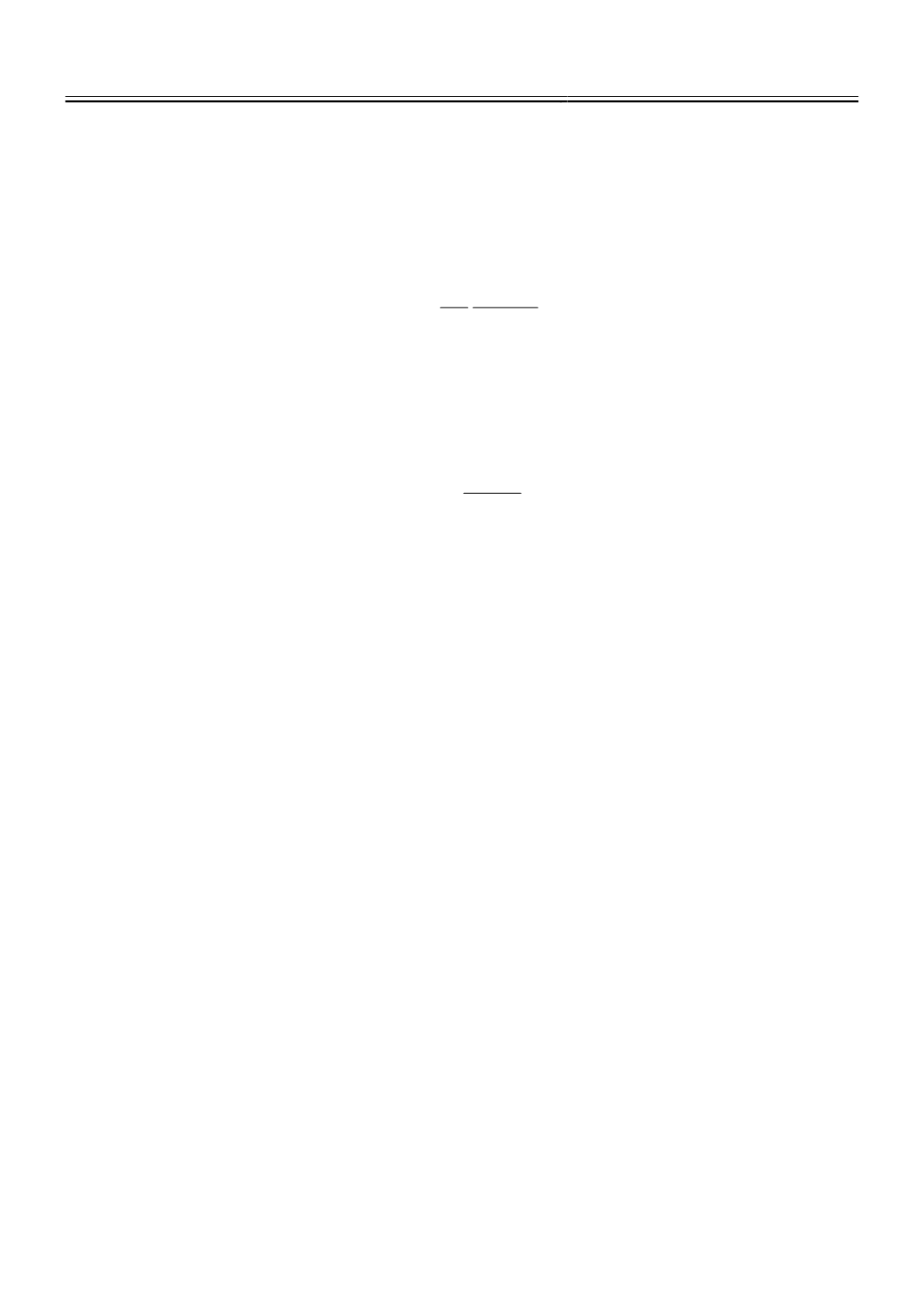
Актуальные проблемы в машиностроении. 2016. №3
Технологическое оборудование,
оснастка и инструменты
____________________________________________________________________
333
h
a
x
Lxh h
/
,
(7)
где
а
h
– степенной показатель формы очага деформации (для роликов принимается а
h
=2);
x
–
текущая координата рассматриваемого сечения.
Схема решения включала два внешних цикла.
На первом цикле была организована процедура расчета параметров процесса в зави-
симости от минимально необходимого числа оборотов обода:
об
пр в
п
об
D
Rn
V
h
n
30
,
(8)
где
h
– суммарное обжатие профиля;
п
V
– скорость подачи верхнего ролика;
в
n
– частота
вращения роликов (об/мин);
об
D
– диаметр обода колеса.
На втором, внутреннем, цикле определялись параметры процесса в течение одного
оборота обода, при этом обжатие на текущем i-ом шаге (например, 15°) определялось по сле-
дующей зависимости
п
пр в
об
об
V
Rn
D
h
i
30
.
(9)
В целом, представленные выше зависимости в сочетании с расчетом параметров сече-
ния заготовки составили полный алгоритм по автоматизированному расчету энергосиловых
параметров процесса профилировки ободьев колес.
Для проверки адекватности предложенной численной математической модели была
разработана конечно-элементная модель процесса. При этом использовалась расчетная схе-
ма, которая представляла собой заготовку и два рабочих ролика с калиброванной бочкой.
Непосредственно моделирование процесса было выполнено для заготовки диаметром 524 мм
из стали 08сп. Модель имела следующие граничные условия: верхний ролик имел одну вра-
щательную степень свободы и перемещения, нижний ролик – только одну вращательную
степень свободы.
Результаты и обсуждение
В результате реализации численной модели были получены зависимости силы профи-
лирования от толщины металла обода колеса (рис. 3,а). Из анализа видно, что с увеличением
толщины листов сила увеличивается. Так, например, при увеличении толщины листа с 3 мм
до 7 мм (в 2,3 раза) сила возрастает с 264 кН до 967 кН (в 3,7 раза). На рис. 3,б представлены
расчетные зависимости силы профилирования от радиуса роликов, при этом видно, что с
увеличением радиуса роликов сила возрастает. При увеличении радиуса ролика с 200 до 400
мм сила возросла в 2,5 раза.
Из проведенных расчетов была определена максимальная сила профилирования, ко-
торая составила 1,2 МН, при этом момент – 3400 Нм, а мощность – 9,7 кВт. Эти данные были
использованы при реконструкции машины ИБО-130. Сила профилирования при конечно-
элементом моделировании составила 1,12 МН, что ниже аналогичного значения, полученно-
го при численном моделировании на 6,7%, что свидетельствует об адекватности предложен-
ной модели и возможности её использования при проектировочных расчетах.