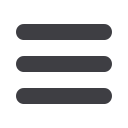
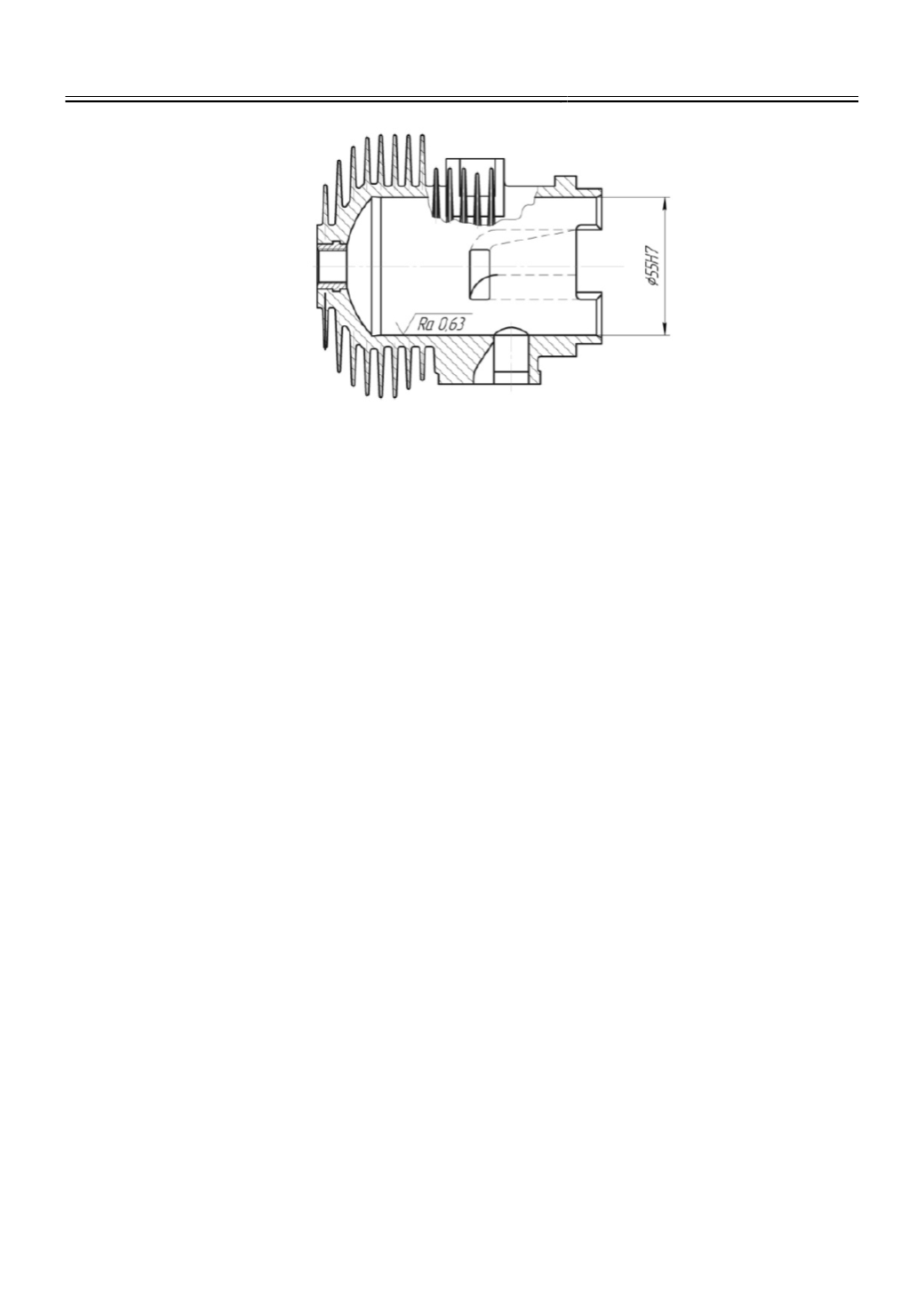
Actual Problems in Machine Building. 2016. N 3
Innovative Technologies
in Mechanical Engineering
____________________________________________________________________
118
Рис. 1.
Тонкостенная корпусная деталь.
Тонкостенные корпусные детали, в целях облегчения массы, изготавливаются литьем
из алюминиевых сплавов. При охлаждении отливок из-за разной толщины стенок, образуется
неоднородная структура, что приводит при обработке к формированию нестабильных
механических свойств поверхности, разной шероховатости и к отклонению размеров и
формы поверхности. Точность формы является одним из важных требований в обработке
базовых отверстий корпусных деталей,
выполняющих функцию направляющих
поверхностей, т.к. к ним предъявляются повышенные требования по износостойкости [1].
Ожидаемая точность обработки является суммарным результатом влияния
многочисленных элементарных погрешностей. Каждая из них, вносит свою долю в общую
погрешность и в это же время опосредованно или напрямую влияет на остальные
элементарные погрешности [2].
Доля различных элементарных погрешностей в общей погрешности для наиболее
распространенных случаев примерно составляет [2]:
• погрешность установки при обработке отверстий данных корпусных деталей:
2...40%;
• погрешности, связанные с упругими деформациями системы технологической
системы: 0...80%;
• погрешности от настройки и износа инструмента: 5.. .40%;
• погрешности от тепловых деформаций элементов ТС: 15.. .70%;
• погрешности формы обрабатываемой поверхности из-за геометрических
погрешностей станка: 1...15%;
В предыдущей работе [3], были проведены исследования и выявлено, что
значительное влияние на общую погрешность обработки формы отверстий оказывают
тепловые деформации. Для тонкостенных деталей с переменной толщиной стенки
погрешности, связанные с тепловой деформацией, могут составлять до 70%. Следовательно,
снижение теплообразования при резании и, соответственно, уменьшение ТД заготовки
возможно, в основном, путем уменьшения режимов обработки, что приводит к снижению
производительности.
Таким образом, необходимо прогнозировать величину тепловой деформации на
стадии проектирования технологического процесса c использованием комплексного подхода,
который состоит из двух этапов: первый этап (вспомогательный) основан на методе
конечного элементного анализа (LS-DYNA), второй (прогнозирующий) этап основана
обучении и построении нейронной сети (Statistica Neural
Networks).