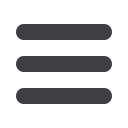
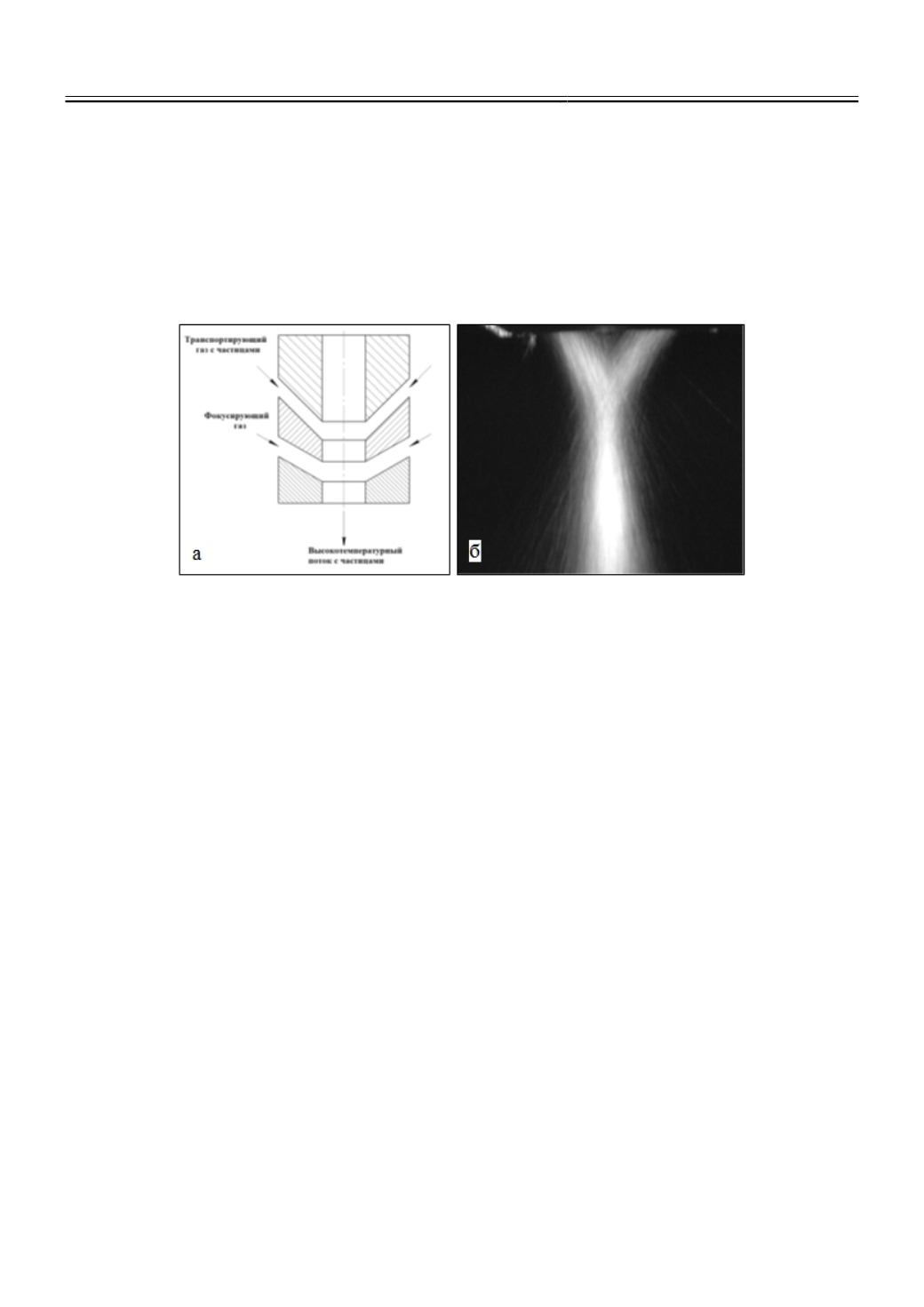
Actual Problems in Machine Building. Vol. 4. N 2. 2017
Innovative Technologies
in Mechanical Engineering
____________________________________________________________________
18
Среднемассовая температура потока воздушной, или азотной плазмы на срезе сопла
плазмотрона – до 7000 К, аргоновой плазмы – до 11000 К, что позволяет обрабатывать не
только легкоплавкие, но и тугоплавкие металлы и керамику.
Плазмотрон укомплектован узлом кольцевого ввода порошка с его газодинамической
фокусировкой (Рис. 2). На конструкцию узла получен патент РФ [6]. Узел кольцевого ввода
обеспечивает равномерный, распределённый ввод порошка в поток термической плазмы, что
существенно повышает производительность и эффективность обработки порошков (по
сравнению с точечным вводом производительность обработки выросла почти на порядок).
Рис. 2.
Узел кольцевого ввода:
а – принципиальная схема кольцевого ввода порошка; б – фотография треков частиц
порошка истекающих из радиально-кольцевой щели узла ввода при холодной продувке [7]
Эксперимент был проведен на медном порошке марки ПМС-1. Порошок был
предварительно просушен для достижения максимальной сыпучести и наименьшей степени
прилипания к стенкам бункера дозатора и каналам узла кольцевого ввода.
После проведения подготовительных работ просушенный порошок засыпался в
бункер дозатора. После чего производился запуск плазмотрона и порошок при помощи
транспортирующего газа, через узел кольцевого ввода, вводился в поток термической
плазмы. Поток фокусирующего газа обеспечивал максимальную концентрацию частиц
порошка на оси потока плазмы.
В качестве плазмообразующего газа использовался воздух, в качестве защитного газа
(завеса анода) – смесь воздуха и небольшого количества пропан-бутана. Пропан-бутан,
распределяясь преимущественно в пограничном слое потока плазмы в канале анода
плазмотрона, связывал кислород воздуха и обеспечивал, таким образом, минимальную
эрозию материала анода. Добавка пропан-бутана в транспортирующий и фокусирующий
газы (основной газ – воздух) обеспечивала минимальное окисление частиц обрабатываемого
порошкового материала.
Таким образом формировался высокотемпературный гетерогенный поток, где и
проходила обработка частиц исходного порошка. При этом на перемещающиеся частицы
воздействовал ряд основных сил, таких как сила тяжести, сила поверхностного натяжения,
сила динамического давления потока плазмы [8]. Сфероидизацию исходного порошка
обеспечивает сила поверхностного натяжения частиц, находящихся в жидкой фазе.
Обработанный порошок собирался в емкость с водой, которая находилась на
расстоянии ~ 1м от среза сопла плазмотрона, где он охлаждался, сохраняя при этом
полученную форму.