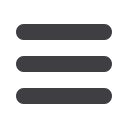
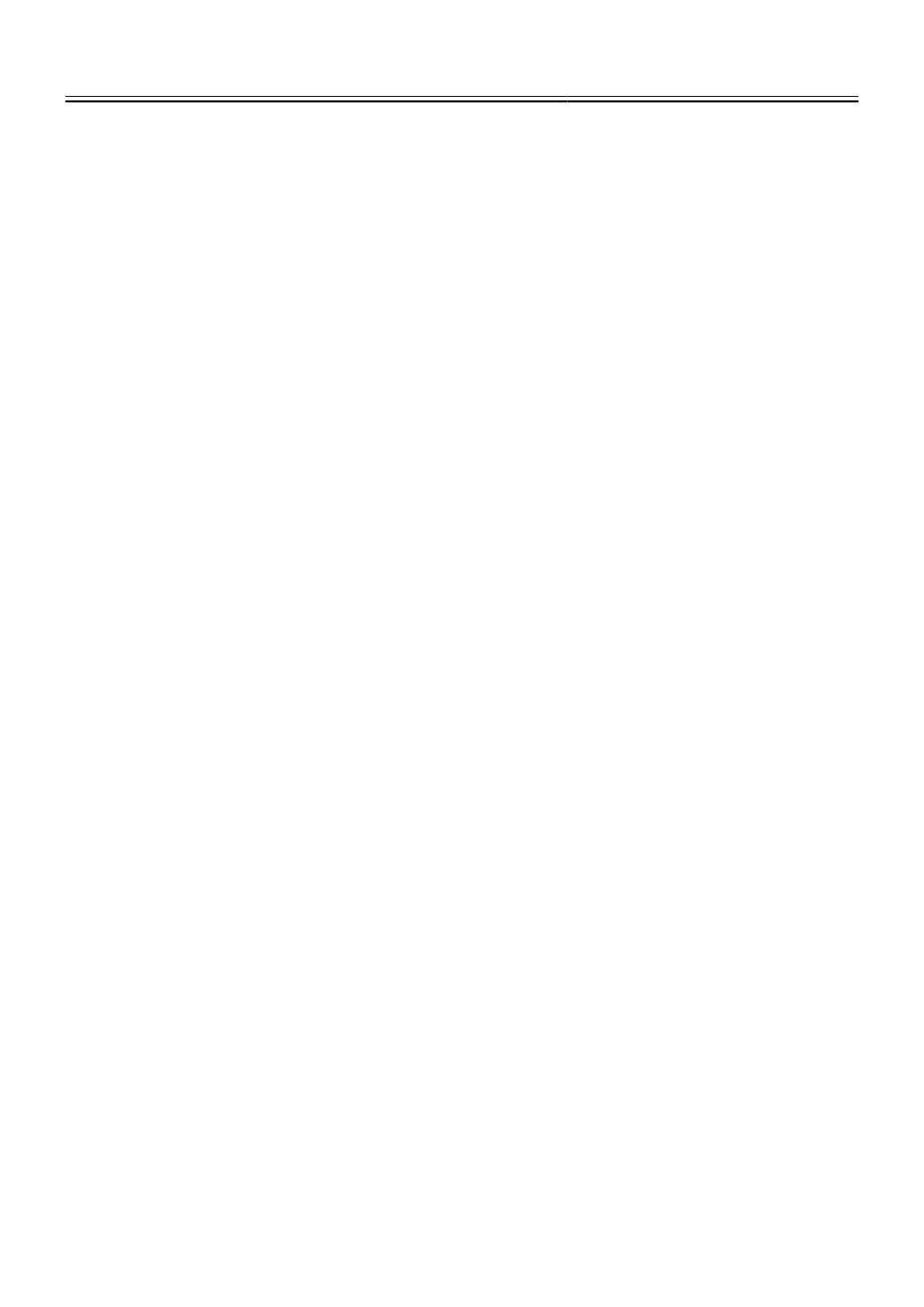
Actual Problems in Machine Building. 2015. N 2
Materials Science
in Machine Building
____________________________________________________________________
348
напряжений в слое покрытия. Так, относительно невысокий уровень адгезионной прочности
при высоких контактных давлениях может являться причиной нарушения сплошности
поверхности плазменных покрытий в виде отслоений и сколов частиц покрытия в процессе
эксплуатации оборудования, что, естественно, ограничивает его технический ресурс.
Традиционные технологии нанесения плазменных покрытий практически полностью
исчерпали свои потенциальные возможности, поэтому в последнее время с целью
повышения качества покрытий все более широкое применение получают так называемые
комбинированные технологии [23-29]. Сущность комбинированных технологий заключается
в повторном высокоэнергетическом воздействии на поверхность покрытий с целью
улучшения их качественных показателей: увеличение адгезионной прочности, уменьшение
пористости, ликвидация нерасплавленных частиц порошка в структуре покрытий,
формирование мелкодисперсной структуры и обеспечение равномерного распределения
микротвердости по глубине упрочненного слоя.
Нами проанализированы технологические возможности основных методов обработки
концентрированными источниками энергии (электродуговой, электронно-лучевой, лазерный,
плазменный и индукционный) [27, 30], которые можно использовать для повторного
высокоэнергетического воздействия на структуру плазменных покрытий. Анализ показал,
что с позиции практического использования в промышленности конкурирующими методами
можно считать плазменную обработку и высокоэнергетический нагрев токами высокой
частоты (ВЭН ТВЧ). Однако индукционный нагрев более предпочтителен. Характерной
особенностью этого процесса является то, что источник нагрева является объемным и
выделение энергии осуществляется на некоторой глубине поверхностного слоя, величина
которого зависит от теплофизических свойств и удельного электрического сопротивления
материала покрытия, а также частоты тока. Кроме того, современные индукционные
установки обладают практически самым высоким коэффициентом полезного действия,
небольшими габаритами и массой, позволяют управлять глубиной температурного
воздействия и обеспечивают высокую скорость нагрева [17].
Ранее нами была выявлена характерная структура износостойких плазменных
покрытий после воздействия ВЭН ТВЧ [17]. Целью настоящей работы является более
глубокое изучение особенностей формирования структуры.
Методика проведения экспериментов
Нанесение плазменных покрытий из промышленного высокохромистого чугуна марки
ПГ-С27 с фракционным размером частиц 50…100 мкм на плоские образцы из стали 20
производили на установке "Киев-7" плазмотроном ПУН-8 мощностью 40 кВт [15]. Режимы
напыления: сила тока дуги плазматрона
I
= 140 А, напряжение
U
= 140 В и дистанция
напыления
L
= 110 мм.
Оплавление поверхности образцов осуществляли на экспериментальной установке,
снабженным приводом главного движения с плавным регулированием скорости. В качестве
источника энергии использовали ламповый генератор модели ВЧГ 6-60/0,44 с рабочей
частотой тока 440 кГц. Процесс нагрева производили по глубинной схеме (глубина
выделения энергии порядка 0,6…0,8 мм) непрерывно-последовательным способом. При
повторном упрочнении использовали индуктор петлевого типа, оснащенный
магнитопроводом марки
N
87 [31, 32]. Удельная мощность нагрева варьировалась в пределах
от 2,8∙10
8
Вт/м
2
до 3,4∙10
8
Вт/м
2
, а скорость перемещения образцов относительно петлевого
индуктора – от 20 мм/с до 120 мм/с.
Металлографические исследования структуры выполняли на растровом микроскопе
марки
Carl Zeiss Axio Observer Alm.