
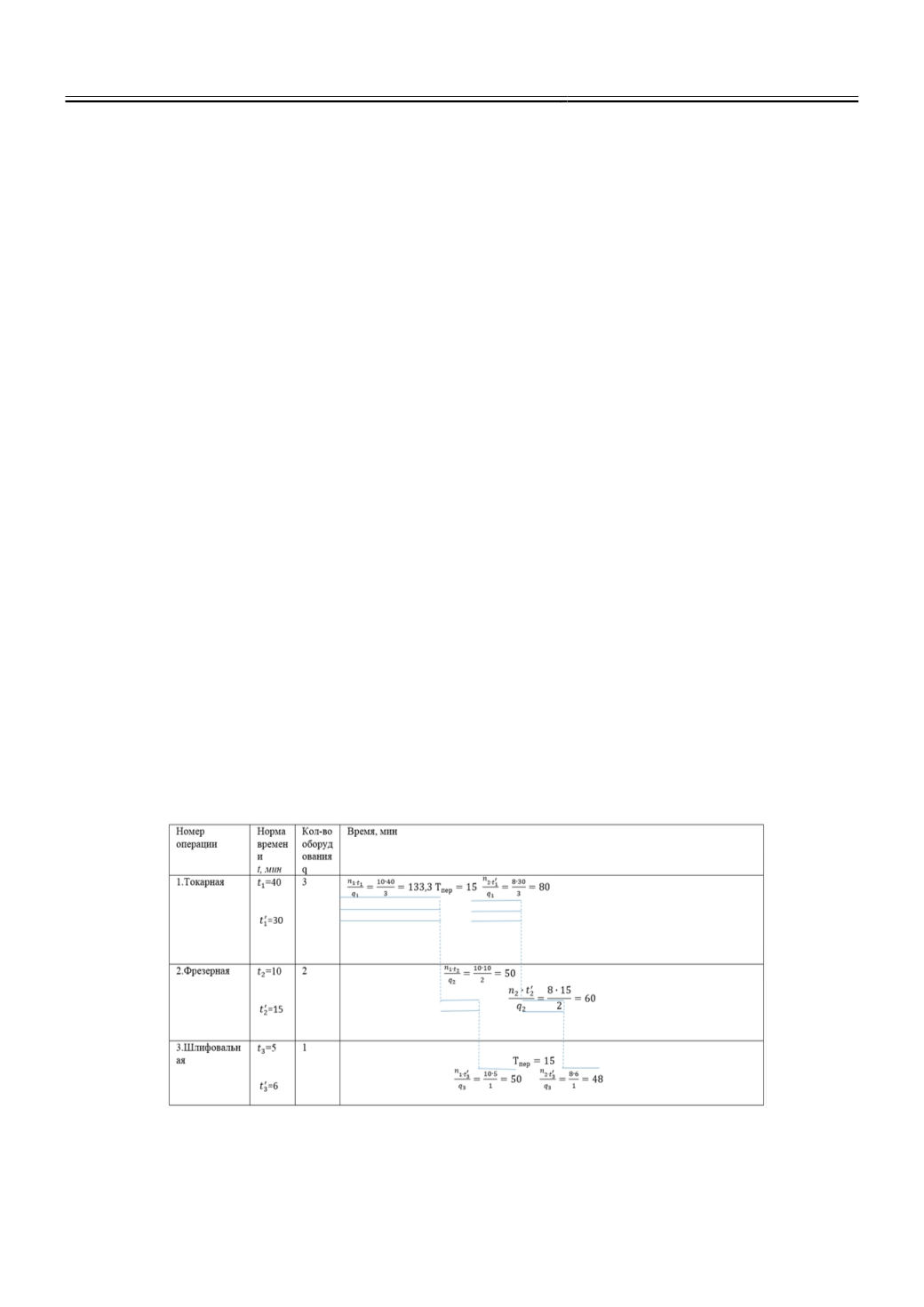
Actual Problems in Machine Building. Vol. 4. N 1. 2017
Innovative Technologies
in Mechanical Engineering
____________________________________________________________________
16
Базируясь на методике укрупненного расчета трудоемкости на основе
квалиметрического анализа деталей, получаемых обработкой резанием [2] разработана
методика квалиметрического анализа деталей при прогнозировании временных затрат на
производство широкой номенклатуры изделий предприятия [2, 4].
Для определения очередности запуска-выпуска групп деталей в производство детали
группируются на основании сходного технологического маршрута, массы, трудоемкости и
месячной программы выпуска. Выбор партий деталей, имеющих одинаковый
технологический маршрут для одновременной обработки в одну смену формируется на
основании заказов потребителей. Задача распределения заданий по выпуску изделий в
различные месяцы ориентирована на директивные сроки выпуска.
Для сокращения номенклатуры одновременно изготовляемых изделий необходимо
разделить месячное задание по декадам с целью загрузки станков в одну декаду
ограниченной номенклатурой, например, не более 5 наименований, соблюдая правило
одинакового технологического маршрута (одинаковой последовательности и количества
операций m). При заданной программе по k-той номенклатурной позиции на декаду месяца
по участку (N
k
) можно рассчитать сменное задание, которое находится делением задания на
декаду (N
k
) на рабочее число дней (при 5 дневной рабочей неделе и односменном режиме
работы предприятия): N
kсм.
= N
k
/8, где 8 – число рабочих дней в декаду.
Отправным критерием при установлении нормативной величины партии должна
служить непрерывность выполнения каждой операции обрабатываемой партии, по меньшей
мере в течение смены. В этом случае, целесообразно принять размеры партий по k-тым
номенклатурным позициям (n
k
), обрабатываемым одновременно, равными (n
k
=n) и наложить
ограничение на размер партии - он должен быть не менее сменного задания, и разница между
ними должна быть минимальна.
Первый вариант запуска – последовательный запуск партий деталей. Предварительно
партии деталей ранжируются по трудоемкости обработки: первой в запуск идет самая
трудоемкая деталь, потом менее трудоемкая и т.д. (рисунок 1).
Предполагается, что в течение смены k-е количество партий разных номенклатурных
позиций будет обрабатываться одновременно на одном и том же наборе оборудования с
переналадкой при переходе от одной партии к другой. При этом варианте загрузка
оборудования будет максимальной, что снизит количество оборудования, но будет иметь
место переналадка в течение смены.
Рис.1.
Последовательный запуск партий деталей в производство [3]
В первом варианте для определения количества задействованного оборудования по
операциям выбираются самые продолжительные по времени операции по ходу