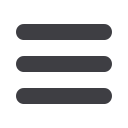
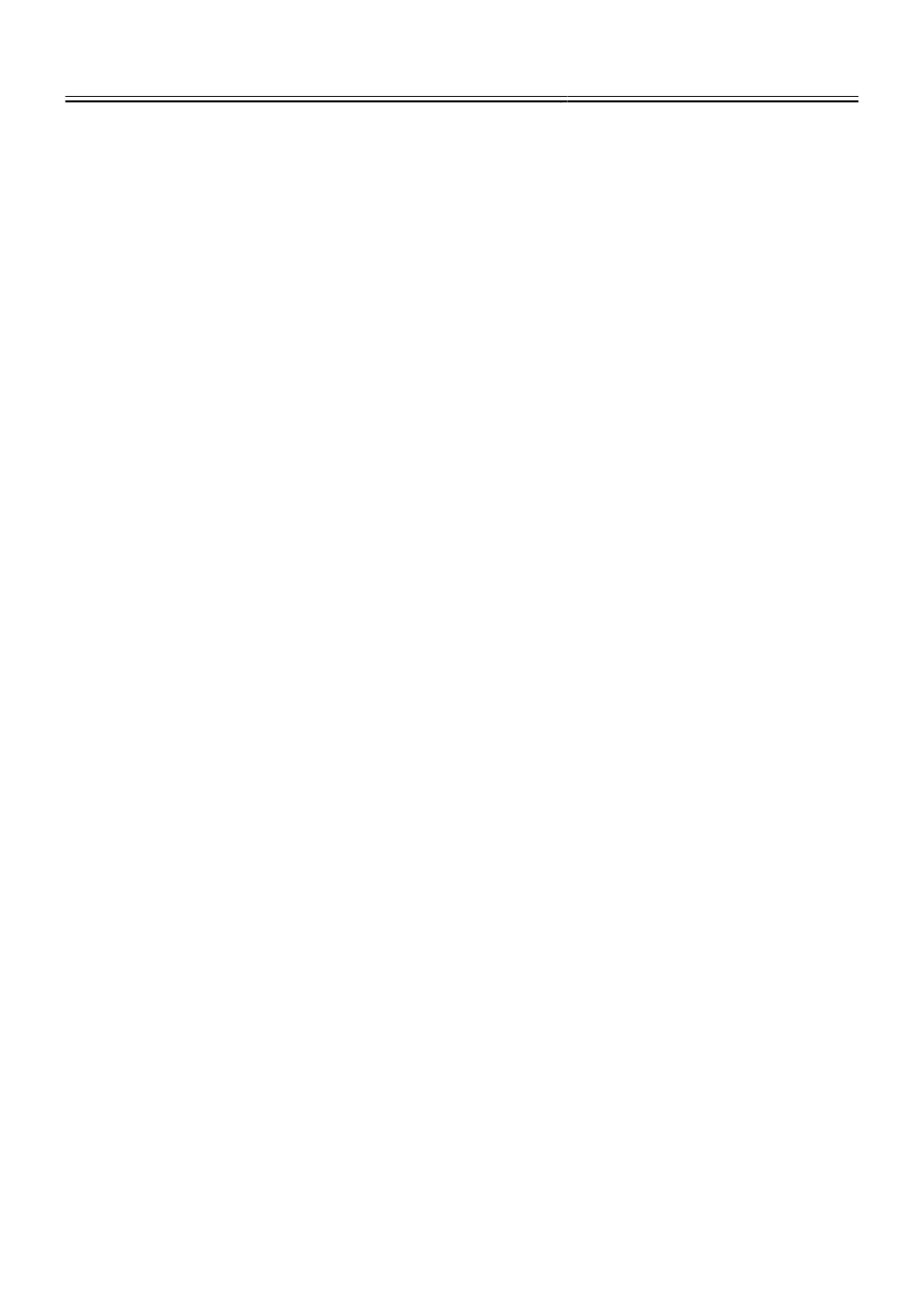
Actual Problems in Machine Building. Vol. 4. N 4. 2017
Innovative Technologies
in Mechanical Engineering
____________________________________________________________________
54
менее 120-150 м/мин). Затем торец втулки 7 прижимается к поверхности детали 8 с осевым
усилием, обеспечивающим эффективный нагрев, (величина минимального удельного
давления зависит от коэффициента трения между торцом инструмента и деталью, а также их
термическими характеристиками). Параметры режима обработки должны обеспечивать
быстрый (в течение 6-12 с.) локальный нагрев детали в зоне контакта с инструментом до
температуры размягчения. При этой температуре (для стали это 900 -1100̊ С) пластичность
металла резко возрастает, а сопротивление пластическому деформированию падает. Нагрев
сопровождается вдавливанием инструмента в заготовку и вытеснением металла на
периферию и в центральное отверстие. На периферию металла вытесняется незначительный
объем металла только в начальный период вдавливания инструмента. При этом образуется
заусенец высотой 1,5-2,5 мм. В дальнейшем нагретый металл выдавливается только в
центральное отверстие инструмента и осуществляется обратное выдавливание.
После внедрения инструмента на заданную глубину, которая определяется
расстоянием между торцом втулки 1 и режущими пластинами зенкера 2, начинается процесс
резания нагретого металла. Это расстояние определяется расчетным или опытным путем
таким образом, чтобы температура в зоне резания была оптимальной. Оптимальная
температура резания выбирается таким образом, чтобы прочностные характеристики
обрабатываемого металла существенно снизились, а режущий инструмент сохранял высокую
стойкость [16, 17]. Диапазон оптимальных температур при обработке стали это 550 - 600̊ С
[16].
Режимы операции
Мощность трения, которая затрачивается на нагрев:
q =2 π ω ∫ p f r
2
dr
где
ω −
угловая скорость;
p −
удельное давление;
f –
коэффициент трения;
r –
радиус
инструмента, который изменяется от внутреннего
R
В
радиуса до наружного
R
Н
.
Если считать, что удельное давление и коэффициент трения постоянны по всей плоскости
контакта:
q =2 π ω p f (R
Н
3
– R
B
3
)
Теплота, затрачиваемая на нагрев металла, приближенно можно оценить, используя
соотношение [18]:
Q
=
c
γ.
ΔT b
(
R
Н
2
+ 0.5 R
Н
x+0,25x
2
)
(1)
где
с –
теплоемкость; γ
–
плотность материала детали;
ΔT –
средняя температура нагрева;
ширина кольца нагретого металла
x = 4√a t
(
a
коэффициент температуропроводности;
b –
толщина зоны нагрева;
t –
время нагрева).
Соотношение (1) можно использовать для оценки требуемой мощности станка: при
низкой интенсивности нагрева увеличивается продолжительность нагрева, а вследствие
теплопроводности растет объем нагреваемого металла, что препятствует реализации способа
образования отверстия. Низкая эффективность нагрева может быть связана не только
недостаточными значениями угловой скорости и удельного давления, но и низким значением
коэффициента трения, что имело место, в частности, при использовании инструмента из
нитридной керамики. Данный способ неприменим и для отверстий малого диаметра (меньше
15 – 17 мм), так как и в этом случае, мощность сил трения оказывается недостаточной для
эффективного разогрева рабочей зоны.
Опытным путем при образовании отверстия диаметром 20 мм в заготовке из стали 45
установлено, что для обеспечения эффективного локального нагрева минимальное число
оборотов должно составлять 2000 - 2200 об/мин (линейная скорость по наружному диаметру
инструмента 126 -140 м/мин), удельное давление на начальном этапе при предварительном
нагреве составило 22 - 27 МПа. О зонах нагрева можно судить по цветам побежалости. При