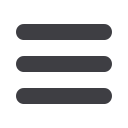
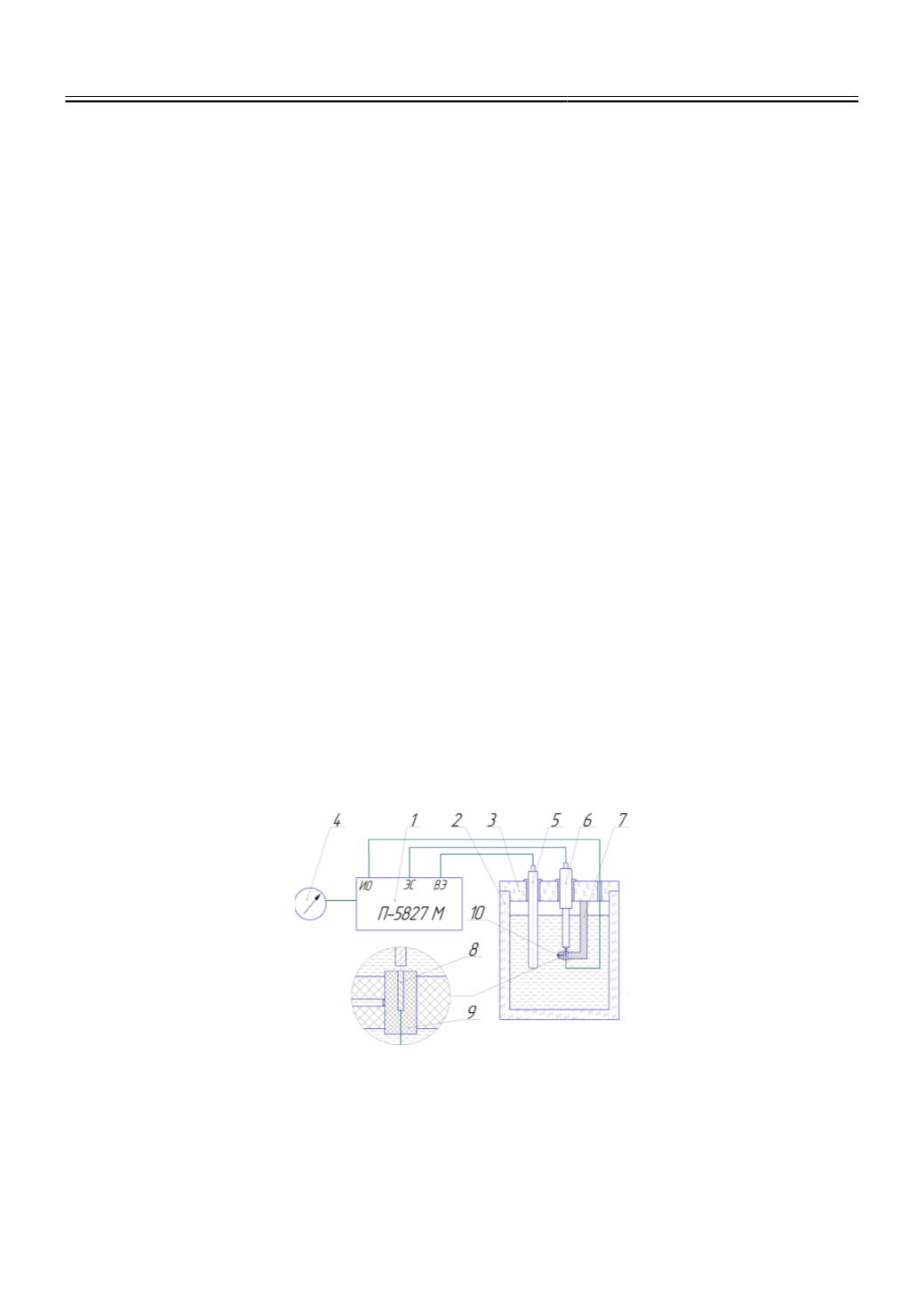
Актуальные проблемы в машиностроении
. Том 4. № 4. 2017
Инновационные технологии
в машиностроении
____________________________________________________________________
23
Одним из возможных методов обработки высокопрочных материалов является
электроалмазное шлифование, которое хорошо зарекомендовало себя при обработке твердых
сплавов, быстрорежущих сталей и износостойких покрытий, благодаря совмещению
процессов электрохимического растворения обрабатываемого материала c процессами
механического резания [7, 8, 9]. Качество и производительность во многом зависит от
особенностей электрохимического растворения обрабатываемого материала в выбранных
составах электролитов [10, 11]. Поэтому для эффективного применения процесса
электроалмазного шлифования при шлифовании износостойких покрытий необходимо
определить особенности электрохимического растворения материала покрытия в различных
составах электролитов.
Методика экспериментального исследования
В качестве материала для нанесения покрытия был выбран порошок ПГ-СР-4.
Согласно ГОСТ 21448-75 покрытия из порошкового материала марки ПГ-СР-4 обладают
твердостью не менее 56,9 НRC, что соответствует требованиям, предъявляемым к деталям,
подвергающихся интенсивному изнашиванию при температурах до 500 °С и воздействию
агрессивных сред. Химический состав порошкового материала ПГ-СР-4: углерод (С) –
0,75%; железо (Fe) – 3.7%; бор (В) – 3,1%; никель (Ni) – является основой; хром (Cr) – 28,5%;
вольфрам (W) – 4,4%; кремний (Si) – 1,0% [12].
Нанесение покрытия марки ПГ-СР-4 осуществлялось методом электронно-лучевой
наплавки в вакууме.
Особенности электрохимического растворения определялись на основе изучения
поляризационных характеристик, устанавливающих зависимость
i
от
φ
.
Для проведения поляризационных исследований образцы заливались в оправки
эпоксидным клеем ЭДП-8 ГОСТ 10587-84, так чтобы растворялся только торец образца,
площадью поперечного сечения 2 мм
2
. В качестве вспомогательного электрода
использовался медный электрод, электрод сравнения – платиновый электрод. На рисунке 3
представлена схема установки для проведения поляризационных исследований. Зазор Δ
между исследуемым образцом и электродом сравнения устанавливался при помощи щупа
ГОСТ 882-75 и составлял 0,5 мм.
Рис. 1.
Схема установки для проведения поляризационных исследований: 1 – потенциостат
П5827М; 2 – емкость для электролита; 3 – крышка; 4 – микроамперметр; 4 – крышка;
5 – вспомогательный электрод; 6 – электрод сравнения; 7 – кронштейн; 8 – исследуемый
образец (рабочий электрод); 8 – кронштейн; 9 – оправка; 10 – крепежный винт.
Известно, что анионный и катионный состав электролита, оказывает существенное
влияние на процесс электрохимического растворения материала [13]. Наиболее