
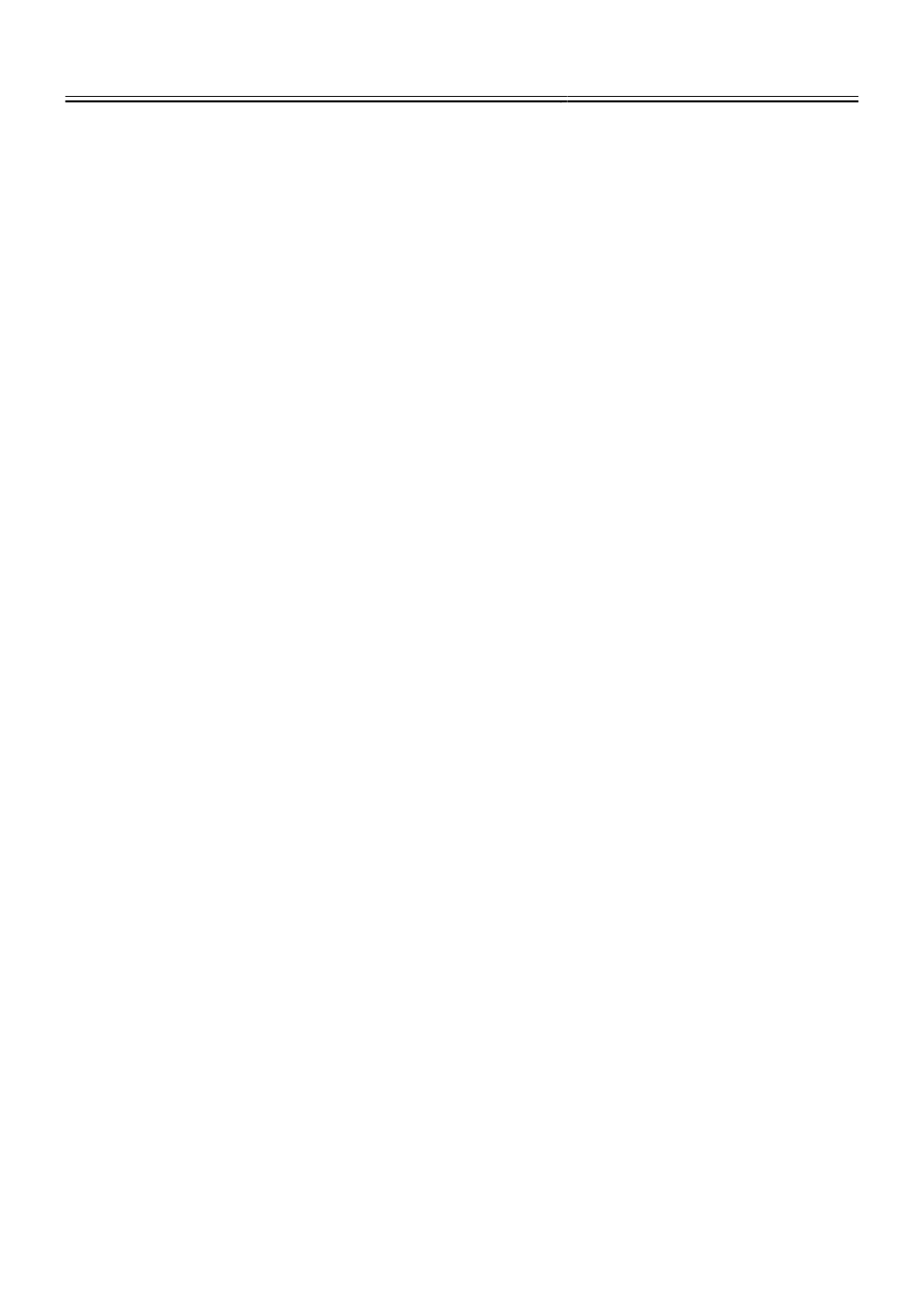
Актуальные проблемы в машиностроении
. Том 4. № 1. 2017
Материаловедение
в машиностроении
____________________________________________________________________
121
station фирмы STIL. Структуру объема модифицированного слоя анализировали методом
поперечного шлифа, для чего образцы разрезали на две части перпендикулярно поверхности
модифицирования. Дефектную структуру материала изучали методами оптической
(микроскоп «Микровизор металлографический µVizo - MET-221»), сканирующей
(сканирующий электронный микроскоп «SEM-515 Philips») и просвечивающей
дифракционной (приборы ЭМ-125 FET Tecnai 2062 TWIN) электронной микроскопии [14-
17].
Элементный состав поверхностного слоя определяли методами
микрорентгеноспектрального анализа (микроанализатор EDAX ECON IV, являющийся
приставкой к электронному сканирующему микроскопу SEM-515 «Philips»). Анализ
фазового состава поверхностного слоя выполняли методами дифракции рентгеновских
лучей (дифрактометр XRD-7000s, Shimadzu, Япония) [18-19].
Результаты и их обсуждение
Основное отличие стали Hardox 450 от широко распространенных износостойких
сталей – это низкое содержание легирующих элементов. За счет этого сталь хорошо
сваривается и обрабатывается. Высокая твердость сталей Hardox достигается за счет
специальной системы закалки листов, которая позволяет получить мелкозернистую
структуру. Суть закалки заключается в быстром охлаждении прокатного листа без
последующего отпуска. По прочности сталь Hardox 450 превосходит другие свариваемые
стали, а по значению ударной вязкости сравнима с обычными конструкционными сталями.
Так, при температуре – 40ºС она имеет гарантированное значение ударной вязкости 30
Дж/см
2
(образец с V-образным надрезом). Предел прочности стали Hardox 450 составляет
1250 МПа, предела текучести – 1000 МПа, относительное удлинение – 15%, относительное
ужение – 63%. Твердость стали в закаленном состоянии составляет 370 HB.
Формирование наплавленного электродуговым методом слоя на поверхности стали
сопровождается слабо контролируемым нагревом материала. Это приводит к протеканию
процесса отпуска закаленного состояния. Отпуск стали приводит к выделению частиц
карбидной фазы (цементита), расположенных в объеме пластин и на их границах. Частицы
имеют игольчатую форму,
характерную для цементита,
образующегося при
низкотемпературном отпуске закаленной стали [20, 21]. Дефектная субструктура пластин
мартенсита представлена дислокациями. Дислокации расположены хаотически, либо
формируют сетчатую субструктуру. Скалярная плотность дислокаций изменяется в весьма
широких пределах – от 3∙10
9
до 6,5∙10
10
см
-2
. Отметим, что в кристаллах мартенсита
закаленной стали скалярная плотность дислокаций составляет 10
11
см
-2
[21, 22]. Нагрев
стали сопровождается разрушением границ кристаллов мартенсита, что особенно
характерно для пакетного мартенсита.
Особенностью фазового состава наплавленного слоя является формирование в
эвтектике пластин борида железа преимущественно состава
Fe
2
B
. Включения борида железа
не содержат в своем объеме дислокационной субструктуры, что кардинально отличает их от
прилегающих слоев α-фазы. Причиной отсутствия дислокационной субструктуры в
пластинах борида железа является их сравнительно высокая твердость (12,5-16,5) ГПа [23,
24]. Характерной особенностью электронно-микроскопического изображения боридов
является наличие в объеме включений большого количества изгибных экстинкционных
контуров.
Разделяющая пластины борида железа
α
-фаза, представлена преимущественно
мартенситом пакетной морфологии, поперечные размеры которых изменяются в пределах
от 30 до 70 нм. В объеме пластин наблюдается дислокационная субструктура сетчатого
типа. Судя по размерам ячеек дислокационных сеток, скалярная плотность дислокаций