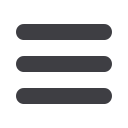
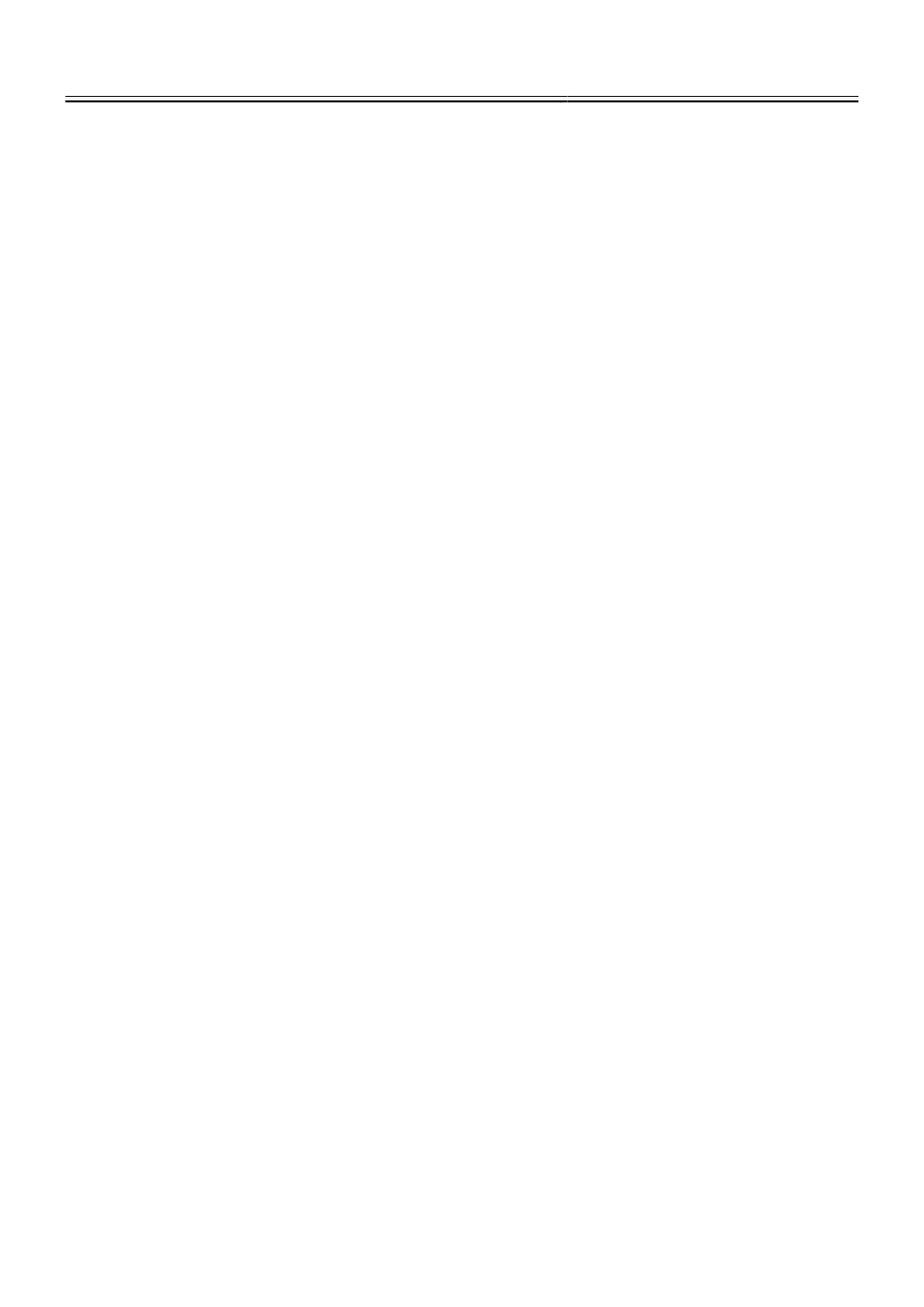
Actual Problems in Machine Building. 2016. N 3
Materials Science
in Machine Building
____________________________________________________________________
462
16] показано, что при легировании танталом формируется карбид тантала (ТаС), который
способствует уменьшению количества C в расплаве и карбид хрома (Cr
7
C
3
) не выделяется.
Добавка оксида ванадия (V
2
O
5
) позволяет сформировать бориды ванадия (VB, VB
2
, V
2
B
3
и
V
3
B
4
), вместо хрупких боридов хрома (CrB
2
и CrB) [5]. Кроме того, образование боридов
ванадия является основной причиной измельчения микроструктуры, что снижает
восприимчивость к растрескиванию. В работе [17] показано, что измельчения частиц борида
хрома CrB можно достичь легированием до 10 вес. % Nb.
Целью данной работы является исследование структурных особенностей плазменных
покрытий системы Ni-Cr-Si-B дополнительно легированных ниобием.
Методика проведения экспериментов
В качестве материала для нанесения покрытий использовали самофлюсующийся
порошок на основе никеля (основа – Ni, 0,4 % C, 15 % Cr, 2 % Si, 2 % В, 3 % Fe), размерами
40…100 мкм и порошок ниобия (93,6 % Nb, 6,4 % Ta), размерами 5…40 мкм.
Смесь порошков (98 мас. % ПР-Н77Х15С3Р2 + 2 мас. % Nb) получали
перемешиванием исходных компонентов в стальном стакане объёмом 250 мл в планетарной
шаровой мельнице Fritsch Pulverisette 6. В качестве мелющих тел использовали стальные
шары диаметром 10 мм. Соотношение масс шаров и порошковой смеси было равным 3:1.
Режимы перемешивания: время измельчения – 30 мин., частота вращения опорного диска –
100 мин
-1
.
Порошок указанного состава напыляли на трубы из низкоуглеродистой стали 20 с
внутренним диаметром 25 мм и толщиной стенки 3 мм. Напыление покрытий проводили в
Институте прикладной и теоретической механики СО РАН на установке плазменного
напыления порошковых материалов «Термоплазма 50-01» с кольцевым вводом порошка. В
качестве плазмообразующего и транспортирующего газа использовали воздух, в качестве
защитного – смесь воздуха и пропан-бутана. Режимы напыления: сила тока – 140 А,
напряжение – 265 В, дистанция напыления – 170 мм. Непосредственно перед напылением
поверхность труб подвергали пескоструйной обработке.
Образцы с покрытиями оплавляли в лабораторных электрических печах камерного
типа (СНОЛ-1,6.2,5.1/11-И3). Режимы оплавления: температура нагрева – 1100 °С, выдержка
– 10 мин., среда охлаждения – воздух. Для сравнения проводили оплавление образцов с
покрытиями только из самофлюсующегося порошка на тех же режимах.
Для проведения металлографических исследований использовали оптический
микроскоп Carl Zeiss AxioObserver A1m и растровый электронный микроскоп Carl Zeiss EVO
50 XVP с микроанализатором EDS X-Act. Образцами для структурных исследований
выступали поперечные микрошлифы, запрессованные в полимерную матрицу и
подготовленные по стандартной методике (шлифование абразивными бумагами и
полирование суспензией, содержащей частицы оксида хрома).
Для травления
микроструктуры покрытий использовали раствор, состоящий из 10 мл HCl, 0.1 мл HNO
3
и 10
г FeCl
3
. Микротвердость структурных составляющих в покрытиях оценивали на приборе
Wolpert Group 402MVD при нагрузках 10 и 25 г.
Результаты исследований
В результате микроструктурных исследований было выявлено, что толщина
полученных покрытий составляет 1200…1300 мкм. Ранее было показано, что материал
самофлюсующихся плазменных покрытий характеризуется наличием слабо- и
сильнодеформированных частиц порошка, а также оплавленных частиц, которые в процессе