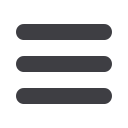

Актуальные проблемы в машиностроении. 2016. №3
Инновационные технологии
в машиностроении
____________________________________________________________________
37
УДК 621.791.55
ВЛИЯНИЕ РАСХОДА ЗАЩИТНОГО ГАЗА НА ФОРМУ НАПЛАВЛЯЕМОГО
ВАЛИКА ПРИ ВОССТАНОВЛЕНИИ ИЗНОШЕННЫХ ДЕТАЛЕЙ
*
Д.А. ЧИНАХОВ
1
, к.т.н. доцент
Е.Г. ГРИГОРЬЕВА
1
, ассистент
Е.И. МАЙОРОВА
1, 2
, аспирант
(
1
ЮТИ ТПУ, г. Юрга,
2
ТПУ, г. Томск)
Чинахов Д.А.-
652055, г. Юрга, ул. Ленинградская д.26,
Юргинский технологический институт
Национального исследовательского Томского политехнического университета,
e-mail:
chinakhov@tpu.ruПриведены способы управления геометрией наплавляемого валика при наплавке
плавящимся электродом. Дана сравнительная оценка геометрических параметров
навариваемого валика для наплавки с традиционной (одноструйной) газовой защитой и
двухструйной. Расчет коэффициентов характеризующих форму наплавленных валиков
подтвердил влияние расхода защитного газа на формирование наплавленного слоя, особенно
при двухструйной газовой защите.
Ключевые слова:
наплавка, защитный газ, наплавляемый слой, газодинамическое
влияние, двухструйная газовая защита.
Введение
В настоящее время проблема срока службы деталей машин и агрегатов, их
долговечности и надежности приобрела весьма большое значение. Срок службы быстро
изнашивающихся деталей определяет рентабельность многих дорогостоящих машин.
Современные тенденции интенсификации производственных процессов, увеличения рабочих
давлений, скоростей, температуры приводят к ускорению изнашивания деталей, и в
сочетании с необходимостью автоматизации производства, делают проблему повышения
долговечности быстро изнашиваемых узлов машин ещё более острой [1].
Восстановить деталь можно с помощью наплавки, нанося расплавленный металл на
поверхность изделия, нагретую до оплавления или до температуры надежного смачивания
жидким наплавленным металлом. Наплавленный металл связан с основным металлом весьма
прочно и образует одно целое с изделием. Толщина наплавленного металла, образованного
одним или несколькими слоями, может быть различной: 0,5 ... 10 мм и более. [2].
Существуют различные способы наплавки: электродуговая наплавка под слоем
флюса, электрошлаковая, вибродуговая, импульсно-дуговая, плазменная, электромагнитная,
лазерная, электроконтактная наплавка [3].
Все перечисленные способы обладают определенными преимуществами, но и имеют
ряд недостатков, сдерживающих их широкое применение.
В настоящее время наиболее распространённым способом восстановления рабочих
поверхностей, является наплавка в среде защитных газов. Процесс характеризует: низкая
*
Работа выполнена при финансовой поддержке РФФИ. № 16-38-00194 мол_а.