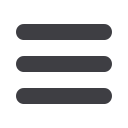
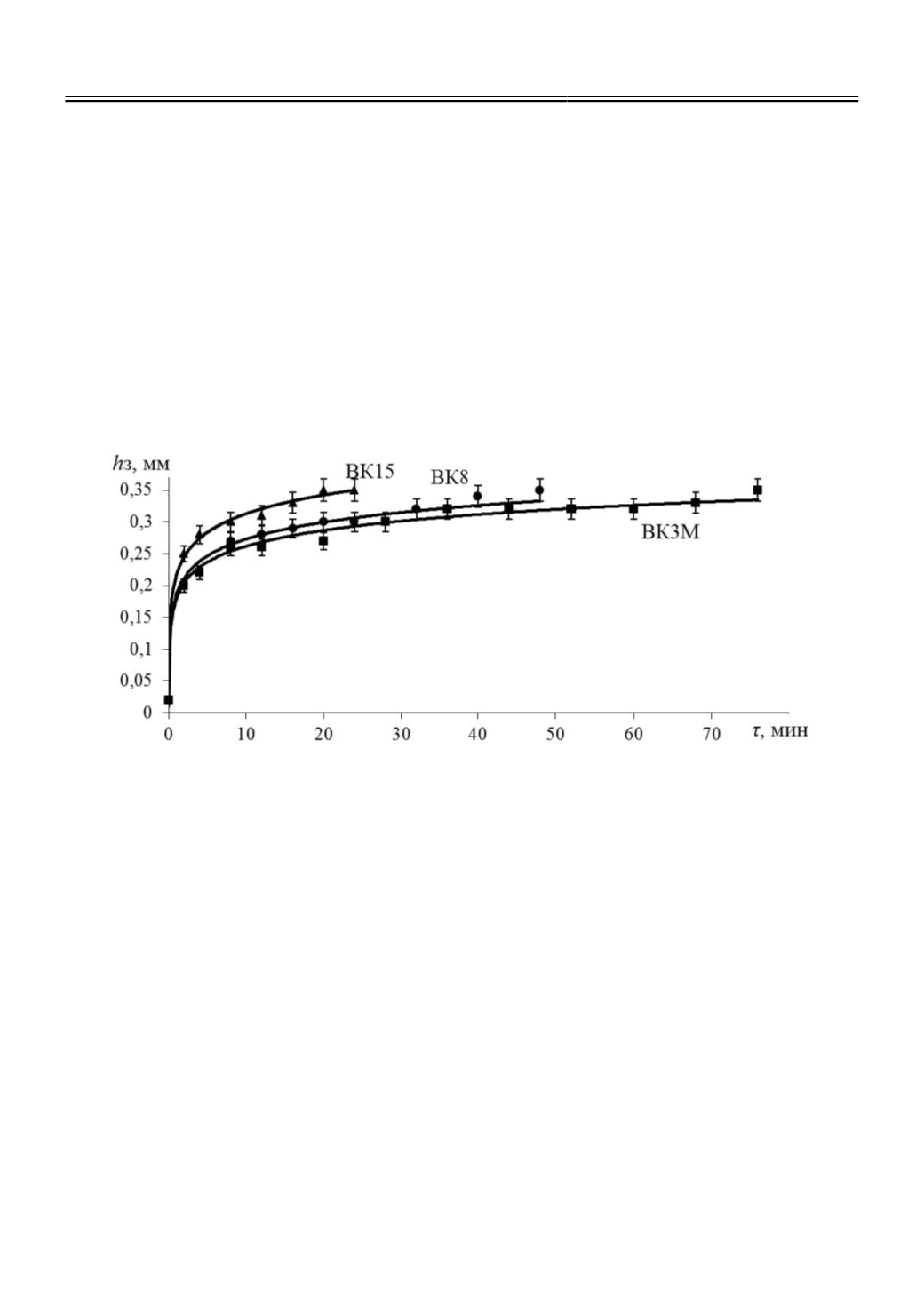
Actual Problems in Machine Building. 2016. N 3
Innovative Technologies
in Mechanical Engineering
____________________________________________________________________
102
имеет более мелкоячеистую структуру, что позволяет уменьшить ворсистость и получить
детали мелких размеров.
Режимы обработки находились в следующих пределах: скорость резания
V
= 45…48
м/с,
S
0
= 1,0…2,0 м/мин (при количестве рабочих зубьев фрезы
z
= 1 при данной скорости
получим подачу на зуб
S
z
= 0,17…0,33 мм/зуб); глубина резания
t
= 0,5…1,5 мм.
Результаты и обсуждение
Одним из факторов, влияющих на качество обработанной поверхности
стекловолокнистых композиционных материалов является износ инструмента.
График (рис. 1) показывает, что уже после двух минут фрезерования размер фаски
износа приобретает высокое значение, характеризующее время приработки инструмента, а
затем увеличивается с меньшей интенсивностью.
Рис. 1.
Зависимость изменения фаски износа по задней поверхности от времени обработки
при S
z
= 0,17 мм/зуб и t = 0,5 мм
Период приработки инструмента, характеризующийся интенсивным износом
режущей кромки, составляет от 2 до 5 минут в зависимости от применяемого твердого
сплава. Далее следует период равномерного износа инструмента, продолжительность
которого различна для исследуемых инструментальных материалов. Сплав ВК15 при данных
условиях обработки выходит из зоны приработки, практически достигая предела, при
котором работа данным инструментом должна быть прекращена в связи с
неудовлетворительным качеством обработанной поверхности и возрастанием
энергетических затрат. Для сплавов ВК8 и ВК3М период приработки составил порядка 2
минут с величиной фаски износа по задней поверхности равной 0,15 и 0,2 мм
соответственно.
Оценка качества поверхности композиционного материала после фрезерования на
различных режимах резания оценено по параметру шероховатости
R
a
с помощью
топографии поверхности на примере твердого сплава ВК3М.
Графики зависимости шероховатости
R
a
от подачи и глубины резания (рис. 2)
показывают, что
R
a
растет с увеличением режимов резания и в условиях получистовой
обработки может составлять менее 3 мкм.