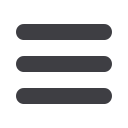
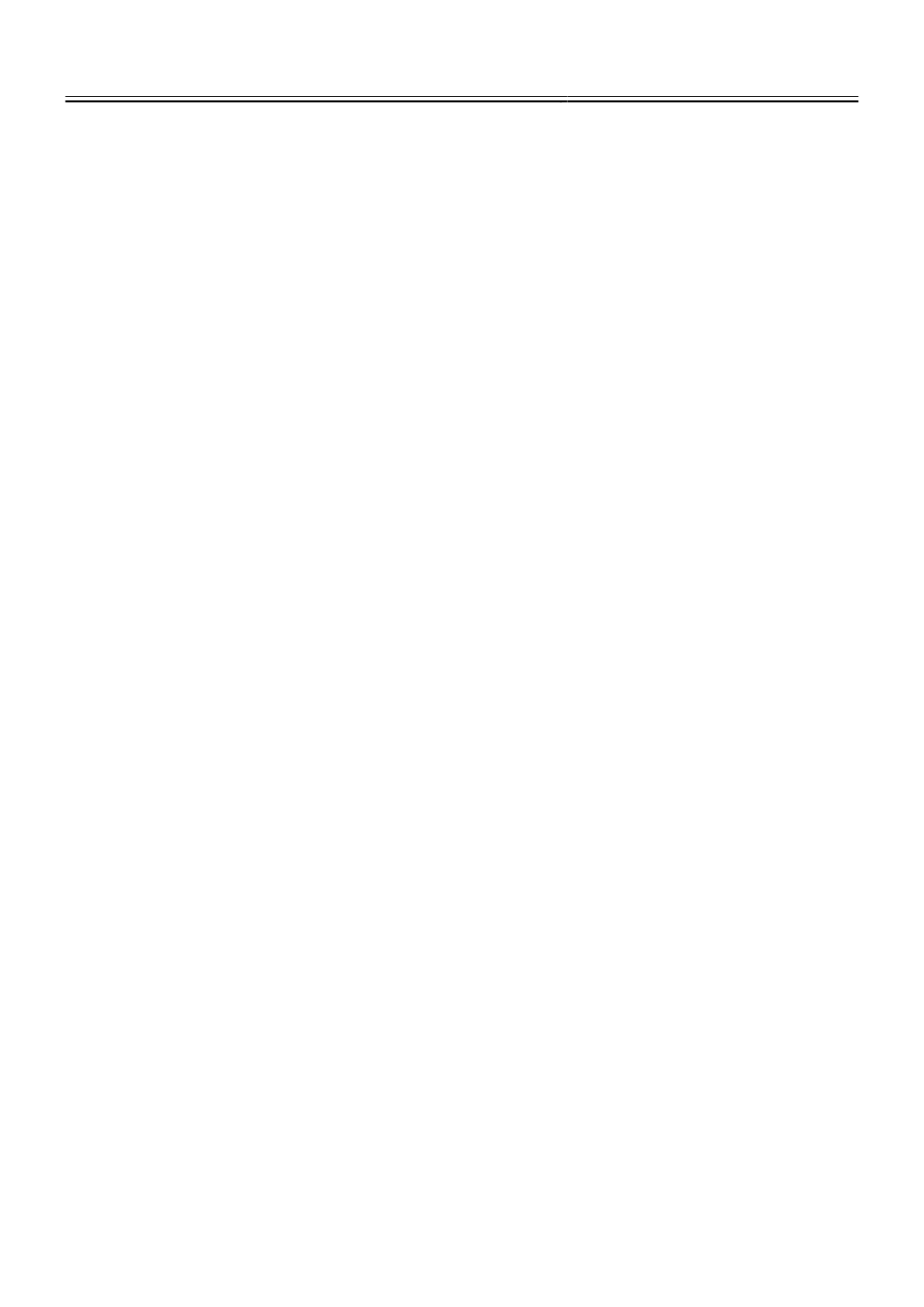
Актуальные проблемы в машиностроении
. Том 4. № 3. 2017
Материаловедение
в машиностроении
____________________________________________________________________
111
SURFACE HARDENING OF TITANIUM BY TiB AND TiC PARTICLES USING
METHODS NON-VACUUM ELECTRON BEAM CLADDING
Chuchkova L.V.
,
Graduate students, e-mail:
L_Chuckova@bk.ruBelov A.S.
,
Student, e-mail:
al_belov98@mail.ruVasilieva V.S.
,
Student, e-mail:
wera.wasiljewa@yandex.ruNovosibirsk State Technical University, 20 Prospect K. Marksa, Novosibirsk, 630073, Russian
Federation
Abstract
Titanium and it’s alloys cannot be used in tribological applications due to low wear resistance.
Promising way to expand the use of these alloys in that area is providing high strength and wear
resistant coating by non-vacuum electron beam cladding.
This paper focused on the study of coatings obtained by cladding with different electron beam
current. Electron beam current changed from 27 to 30 mA, other technological parameters were
fixed. During investigation, the following studies were conducted: optical microscopy, X-ray
diffraction analysis, fixed and against loose abrasive particles friction tests, microhardness tests. X-
ray diffraction analysis has shown that coatings contain of α-titanium (α'-titanium), titanium boride
and titanium carbide phases. Optical microscopy has shown that coating is represented by titanium
matrix reinforced by titanium boride and titanium carbide particles. Undissolved boron carbide
particles where found near heat-affected zone. Depending on beam current coating thickness range
from 1.2 to 1.6 mm. Maximum microhardness value (5900 MPa) for alloyed layers where achieved
by electron beam current 27 mA. Wear resistance increased 1.85 and 2.5 times during fixed and
against loose abrasive particles friction tests respectively in comparison to commercially pure
titanium.
Keywords
Electron beam cladding; titanium; tribological properties; titanium boride; titanium carbide;
microstructure