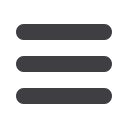
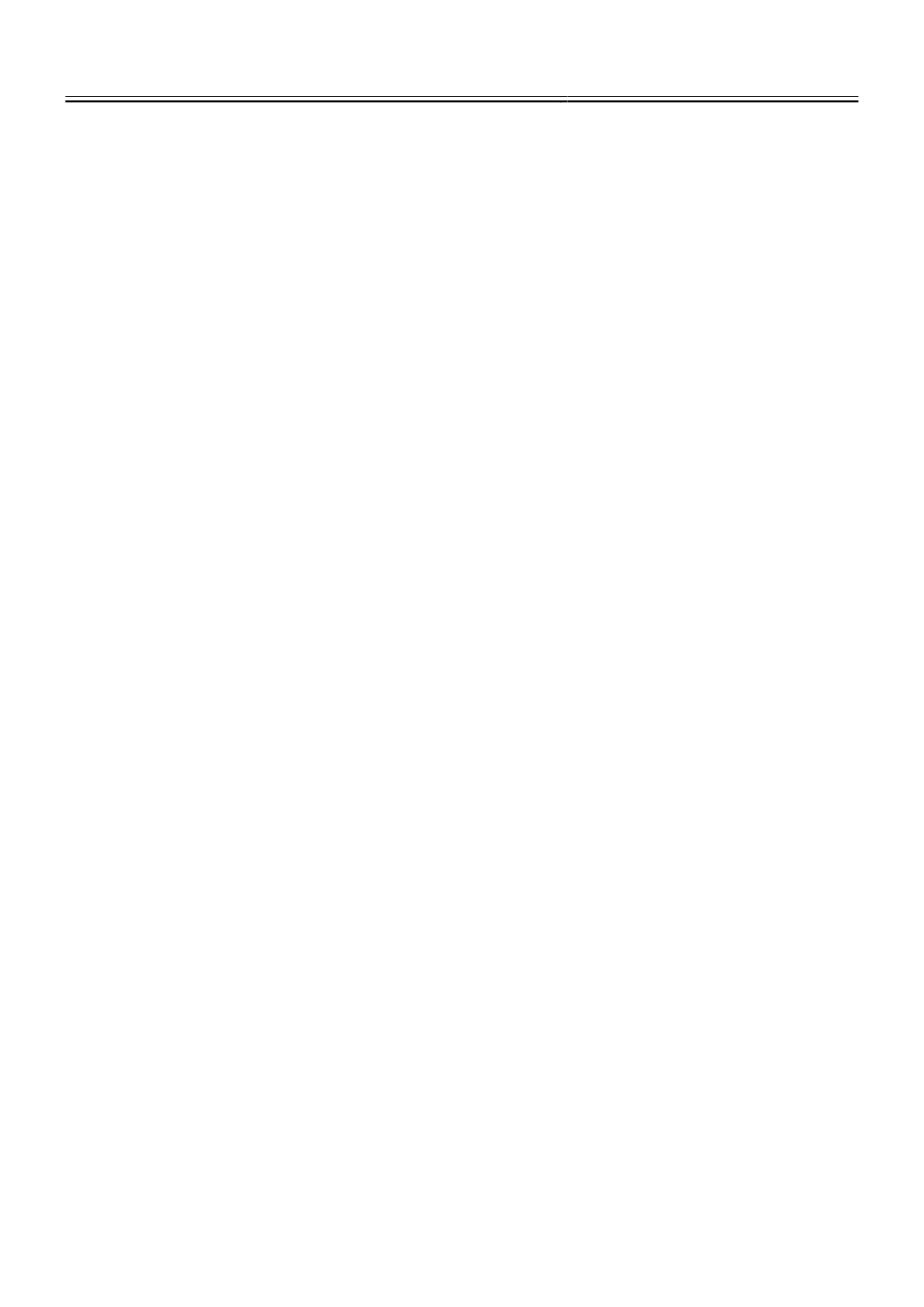
Actual Problems in Machine Building. 2015. N 2
Materials Science
in Machine Building
____________________________________________________________________
364
Целью настоящей работы является анализ закономерностей модификации структуры,
формирующейся в поверхностном слое силумина, подвергнутого облучению
высокоинтенсивным импульсным электронным пучком и последующим многоцикловым
усталостным испытаниям до разрушения.
Материал и методика исследования
Усталостные испытания силумина марки АК12 [9] проводили на специальной
установке по схеме циклического асимметричного консольного изгиба [10]. Образцы имели
форму параллелепипеда с размерами 8х14х145 мм. Имитация трещины осуществлялась
надрезом в виде полуокружности радиуса 10 мм. Температура испытаний 300 К, частота
нагружения образцов изгибом составляла 15 Гц при нагрузке 10 МПа.
Облучение поверхности образцов, приготовленных для усталостных испытаний,
осуществляли на установке «СОЛО» (ИСЭ СО РАН) [6] при следующих параметрах: энергия
электронов 16 кэВ; частота следования импульсов 0,3 с
-1
; длительность импульса пучка
электронов 50 мкс и 150 мкс; плотность энергии пучка электронов (10…25) Дж/см
2
;
количество импульсов воздействия 1, 3, 5. Облучали лицевую поверхность образцов, т.е.
поверхность образца, находящуюся над надрезом, имитирующим трещину. На каждый
режим облучения испытывали не менее 5 образцов. Исследования поверхности облучения и
разрушения осуществляли методами оптической и сканирующей электронной микроскопии.
Результаты эксперимента и их обсуждение
Структура силумина перед облучением электронным пучком (структура исходного
состояния) характеризуется наличием сравнительно крупных (от десятых долей до десятков
микрометра) включений кремния преимущественно пластинчатой морфологии.
Облучение поверхности силумина интенсивным импульсным электронным пучком
субмиллисекундной длительности воздействия в зависимости от плотности энергии пучка
электронов сопровождается оплавлением поверхности образца (рис. 1,
а, б
), либо
плавлением поверхностного слоя материала некоторой (единицы – десятки микрометров)
толщины (рис. 1,
в, г
).
В первом случае процесс модификации пластин кремния сопровождается
формированием многочисленных микропор, расположенных вдоль границы раздела
пластина/матрица, и микротрещин, расположенных в пластинах кремния (рис. 1,
б
).
Очевидно, что при последующих испытаниях на усталостную долговечность пластины
кремния будут являться концентраторами напряжений (источниками микротрещин). Во
втором случае структура поверхностного слоя по морфологическому признаку кардинально
отличается от структуры исходного образца и образца, облученного в режиме оплавления
поверхности (рис. 1,
а, б
). На поверхности облучения формируется однородная структура
зеренного типа (рис. 1,
в, г
). Концентраторы напряжений, способные являться источниками
разрушения образца, на поверхности облучения не обнаруживаются.
Выполненные нами испытания выявили существенную зависимость величины
усталостной долговечности от режима облучения поверхности образцов силумина. При
облучении по режиму, приводящему к частичному оплавлению поверхности образца (рис. 1,
а, б
), усталостная долговечность в отдельных случаях была ниже усталостной долговечности
исходных образцов. При облучении в режиме устойчивого плавления поверхностного слоя с
формированием на поверхности структуры зеренного типа с глобулярными включениями
кремния (рис. 1,
в, г
) усталостная долговечность образцов силумина превышала усталостную
долговечность исходного материала более чем в 3,5 раза.