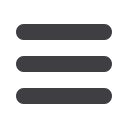
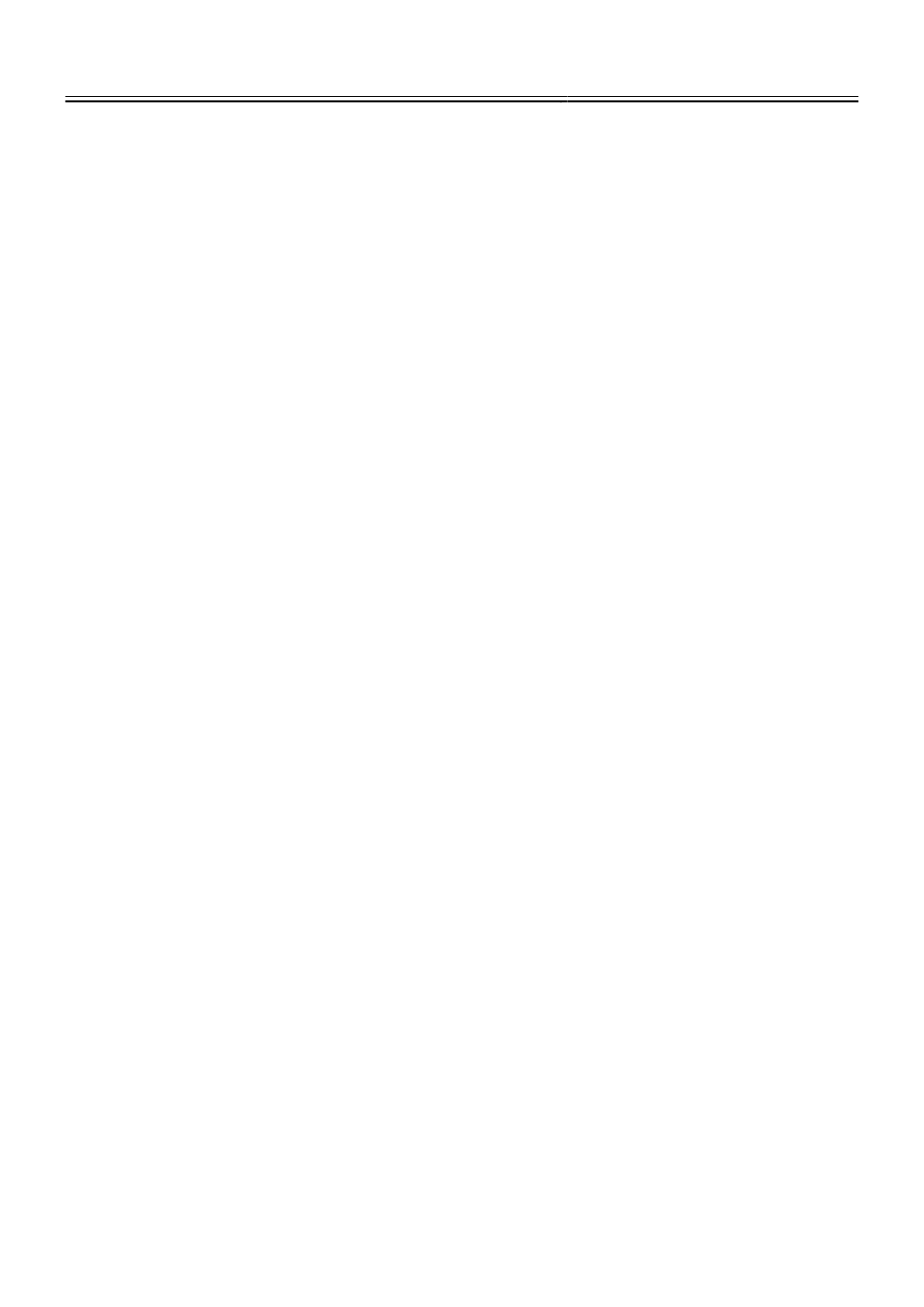
Актуальные проблемы в машиностроении. 2015. №2
Материаловедение
в машиностроении
____________________________________________________________________
389
предупреждает образование травильных трещин, так как уменьшает интенсивность
выделения водорода.
Результаты и обсуждение
Факторы,
способствующие
улучшению
технологичности
микроструктуры
высокохромистых ШСХД:
Дополнительное легирование молибденом и ванадием способствует некоторому
улучшению распределения карбидной фазы, расширяет температурные интервалы
аустенизации и несколько повышает прочностные свойства. Положительное влияние на
основные и технологические характеристики высокохромистых сталей оказывает снижение
концентрации углерода до 1,2 – 1,7%, но и в этом случае сохраняется склонность к
повышенному хрупкому разрушению.
Уменьшение концентрации хрома (стали типа Х6ВФ) также приводит к
формированию более благоприятных структур и возрастанию устойчивости против хрупкого
разрушения, именно потому, в производстве при подходе к выбору штамповой стали,
предпочитают марки с содержанием хрома до 5 – 6 % , и с содержанием углерода до 0,8 – 1,1
%, с более благоприятным характером карбидной фазы, но и с меньшей износостойкостью,
однако, в отличие от Х12МФ, это сопровождается понижением сопротивления истиранию.
Исключением является сталь Х6Ф4М, превосходящая по износостойкости все стали
рассматриваемой группы, однако недостатком её является пониженная шлифуемость,
ограничивающая возможности широкого применения этой стали при применении абразивов
обычного типа [4].
Необходима разработка технологического процесса, учитывающего каждый
фактор, приводящий к дефектам в структуре, на соответствующем этапе, от выплавки стали
до финишной обработки штампа.
Выводы
Таким образом, ряд существенных недостатков иных видов штамповых сталей
вынуждает обращаться к зарекомендовавшей себя высокохромистой стали Х12МФ, и
объясняет необходимость разработки технологии производства штампов из сталей такого
рода, устраняющей либо уменьшающей возникновение дефектов, с учетом таких факторов:
Контроль соответствия поставляемого металла ГОСТу 5950 – 2000, в
особенности, балла карбидной неоднородности, который должен соответствовать, в
зависимости от диаметра прутка, от 4 до 7, и величину зерна аустенита, которая не должна
превышать 8 - 9 баллов.
Соответствие фактического химического состава стали нормативному, в случае
существенных отклонений от ГОСТ 5950 - 2000, требуется коррекция режимов
термообработки.
Предварительная термообработка для предотвращения появления трещин,
гомогенизация и контроль режимов закалки и отпуска.
Шлифовка хорошо отпущенной стали, со снятием за каждый подход слоя
небольшой толщины, без больших давлений. Сразу же после шлифования - дополнительный
отпуск. При травлении применять ингибиторы.
Содержание ванадия и молибдена способствует измельчению зерна аустенита.
При этом ванадий более эффективен, чем молибден, существенно понижая чувствительность
стали к перегреву, и улучшая распределение частиц избыточной карбидной фазы. Поэтому,